Service and Capability
Engineering Service on Foil Bearing Development
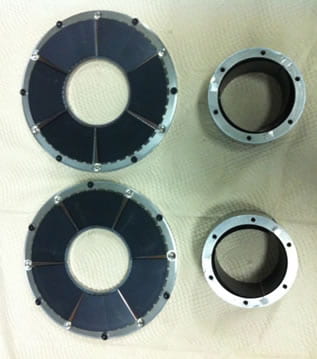
- Core competency of our team is thorough knowledge and know-how on manufacturing process of foil bearings and their operating characteristics.
- UTA helped many companies to develop oil-free turbomachinery program through facilities and resources available at Turbomachinery and Energy Systems Laboratory (partnered with Bellkim Energy, LLC) by providing cost-effective engineering service and technology transfer program. Manufacturing method of foil bearings and tooling designs are usually provided to our customers through technology licensing program
- Based on extensive experience of many different bearing sizes and unique scaling law developed internally, scaling up/down of existing foil bearing design is accomplished without design/test iterations. All our foil bearings applied to the commercial products are from initial prototype bearing without any further design change during entire development period, which often takes a few years.
Engineering Service on Test Rig Design
Depending on their applications, foil bearings need a sequence of unique tests before applying them to final systems. From years of onsite test support of various high speed turbomachinery, our team offers the best solutions from a simple component level test to full scale rig/actual system tests.
Engineering Service on Analysis
Typical rotordynamic analyses using linear stiffness and damping coefficients of the foil bearings do not provide accurate prediction of rotordynamic behavior of foil bearing-supported rotors. Our team offers state-of the art non-linear transient rotordynamic analyses along with dynamic reaction forces from the foil bearings. The method is a little more time-consuming than traditional methods, however, it provides unparalleled accuracy.
Thermal management of foil bearings are equally important. Our team developed the most advanced secondary flow analysis software which can predict pressure and temperature of entire secondary cooling air flow passages including foil bearing static/dynamic performance within the secondary flow passage. Several companies benefited our engineering service to optimize thermal management of the bearings minimizing the cooling air flow rate.